Common Misconceptions About Powder Coating Oven Warm-Up Procedures
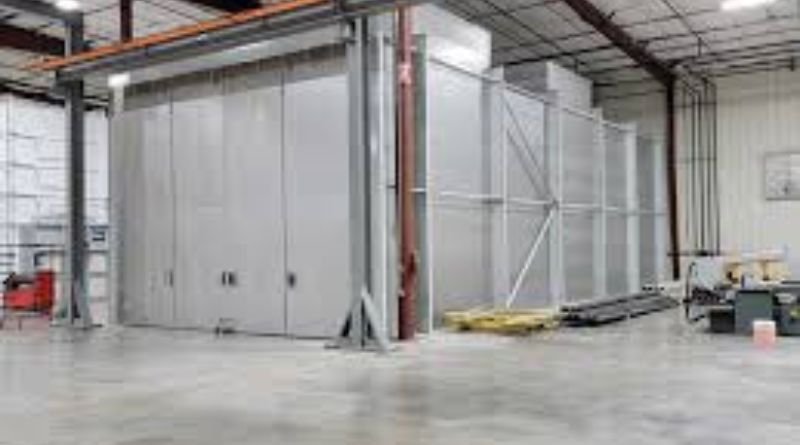
The process of warming up a powder coating oven might seem straightforward, but there are several myths out there that can lead to costly mistakes. These misconceptions often revolve around how warm-up times, temperatures, and heating techniques can impact the quality and efficiency of your work. Let’s set the record straight and debunk some of the most common myths about powder coating oven warm-up procedures.
Faster Warm-Up Equals Better Efficiency Every Time
It might seem like cranking up the heat to warm up a powder coating oven faster would be the most efficient route, but that’s not always the case. While speeding up the warm-up time can seem like a time-saver, it often leads to uneven heating throughout the oven. This can result in cold spots, which can cause the powder coating to cure improperly on certain parts. The goal is to achieve even, consistent heating so that every batch comes out with the same high-quality finish.
In fact, pushing the oven to heat up too quickly can put unnecessary strain on the heating elements. Over time, this extra wear and tear can shorten the lifespan of the equipment, leading to higher maintenance costs and more frequent repairs. Instead of focusing on speed, it’s better to prioritize even heating for better long-term results. Powder coating ovens perform their best when warmed up at a steady, controlled pace.
Uniform Heating Isn’t Necessary for Small Batches
Another common misconception is that if you’re only working with a small batch of parts, you can get away with uneven heating. The logic seems to be that small batches are easier to handle and don’t require as much attention. However, this approach often leads to inconsistent results in the coating process.
Even with small batches, uniform heating in powder coating ovens is essential. Inconsistent temperatures can cause certain parts of the batch to overheat, while others may not cure fully. This results in a lower-quality finish, and you may even have to redo the batch entirely, wasting both time and materials. No matter the size of the batch, consistent heat distribution is always key to achieving the best results.
Preheating Isn’t Critical for Thick Metal Substrates
Some may believe that thick metal parts don’t need the oven to be fully preheated before the powder coating process begins. The idea is that since the metal is dense, it will eventually reach the right temperature anyway. This myth can lead to poor adhesion of the powder, as the initial low temperatures prevent the coating from sticking properly to the metal surface.
For thick metal substrates, preheating the powder coating oven is just as important, if not more so. It ensures the metal reaches an even temperature before the powder is applied, allowing for proper adhesion and smooth coverage. Without preheating, you run the risk of uneven curing, which can result in a less durable finish and potential peeling or cracking over time. Ensuring the oven is fully warmed up before starting the process guarantees a professional finish that lasts.
One Temperature Fits All Powder Coating Projects
There’s a widespread belief that one temperature can work for all powder coating projects. While it might be easier to keep the oven at a single temperature setting, this myth can lead to serious issues depending on the type of powder and material you’re working with. Different powders and substrates require specific temperature settings to achieve optimal results.
For example, certain powders need higher temperatures to properly cure, while others may degrade if exposed to too much heat. Similarly, thinner metal parts may heat up too quickly at higher temperatures, leading to over-curing or even warping. Powder coating ovens should always be adjusted based on the specific requirements of the project to ensure the best finish possible.
Skipping Initial Warm-Up Won’t Affect Long-Term Oven Performance
Some users think that skipping the initial warm-up phase to save time won’t impact the oven’s long-term performance. However, this couldn’t be further from the truth. Skipping this step can cause long-term damage to the heating elements and other critical components in the powder coating oven.
When an oven isn’t allowed to warm up properly, it can lead to thermal shock in the heating elements. This can result in reduced efficiency and even shorten the lifespan of the oven. Regularly allowing the powder coating oven to warm up fully before each use ensures that it operates at peak performance for years to come. The warm-up phase is not just a formality; it’s an important step in maintaining the oven’s longevity.
Higher Initial Temperatures Accelerate the Entire Curing Process
The myth that turning up the heat at the beginning of the process will speed up the curing process is a common misconception. While it might seem like a good idea to blast the oven with higher temperatures to get the job done quicker, it often leads to uneven curing and can damage the powder coating itself.
When you start at a higher temperature, the surface of the part may cure too quickly, leaving the underlying layers uncured. This results in a finish that looks complete on the outside but is weak underneath, compromising the durability of the coating. Powder coating ovens are designed to follow a specific heating curve, gradually bringing the parts up to temperature. Sticking to the recommended temperature ensures the powder coating cures uniformly and provides a durable, high-quality finish.